Water Pollution from Manufacturing Processes
The dirty secret of auto manufacturing isn't just water use - it's what gets put back. Wastewater often contains toxic cocktails of heavy metals, oils, and chemical residues from painting and treatment processes. In developing nations, some plants still discharge this untreated, turning nearby rivers into industrial sewers. Even in regulated markets, accidental spills and permitted discharges add up to significant contamination.
Recent studies found alarming concentrations of chromium, nickel, and zinc downstream from major plants. These metals accumulate in fish, enter food chains, and eventually reach human consumers. The industry's solution - water treatment plants - often falls short, as many facilities prioritize cost over comprehensive filtration. Some plants have adopted zero-liquid-discharge systems, but these remain the exception rather than the rule.
Water Conservation Strategies for Auto Manufacturers
Forward-thinking manufacturers are proving that dramatic reductions are possible. One German plant slashed water use 30% by installing smart sensors that adjust flow rates in real-time. Another breakthrough involves dry machining - using specialized tools that eliminate coolant needs entirely. Perhaps most promising are closed-loop systems that recycle water dozens of times before final treatment.
The biggest savings often come from rethinking entire processes rather than incremental improvements. Some plants now use laser cleaning instead of water blasting, while others have redesigned painting systems to capture and reuse overspray. These innovations prove that with proper investment, the industry could halve its water footprint within a decade.
The Role of Recycling and Material Selection
Material choices create ripple effects through a vehicle's water footprint. Virgin aluminum production ranks among the most water-intensive industrial processes, while recycled aluminum cuts water use by 95%. Similarly, producing synthetic leather consumes far less water than traditional hides. Some manufacturers now prioritize these alternatives, though cost considerations often slow adoption.
The circular economy presents even greater potential. BMW's secondary first approach - using recycled materials whenever possible - has become an industry benchmark. Their i-series vehicles contain up to 30% recycled plastics and 50% recycled aluminum, dramatically reducing embedded water. As recycling technologies improve, these percentages will only climb.
Supply Chain Considerations and Collaboration
A car's true water footprint extends far beyond the assembly plant. Steel mills, rubber plantations, electronics suppliers - each contributes significantly. Some tire manufacturers consume 100 gallons per tire just in cooling processes. Recognizing this, leading automakers now require suppliers to disclose and reduce water usage, with some even providing technical assistance.
Tesla's supplier scorecard system exemplifies this trend, grading partners on water efficiency alongside cost and quality. Such initiatives prove that only through full supply chain engagement can meaningful reductions occur. The next frontier involves collaborating with raw material producers to develop less water-intensive extraction methods.
The Economic and Societal Benefits of Water Conservation
Beyond environmental benefits, water efficiency delivers compelling business advantages. Ford's aggressive conservation program saved $5 million annually while reducing water use 62% since 2000. Similarly, Toyota's water recycling initiatives helped several plants achieve near-self-sufficiency, insulating them from droughts and water restrictions.
These savings multiply when considering risk mitigation. As climate change intensifies water scarcity, factories in water-stressed regions face operational disruptions. Proactive companies gain competitive advantage through reliable production and positive community relations. Consumers increasingly reward this foresight - surveys show water stewardship now influences purchasing decisions nearly as much as fuel efficiency.
Water-Efficient Processes in Component Manufacturing
Minimizing Water Usage in Molding
Injection molding operations have traditionally been water hogs, with cooling systems running continuously. Modern approaches challenge this paradigm. Some plants now use phase-change materials that absorb heat without water, while others employ precision temperature controls that minimize cooling needs. The most advanced facilities combine these with AI-driven process optimization, reducing water use while improving part quality.
Implementing Water Recycling Systems
Closed-loop systems represent the gold standard, but their implementation requires careful planning. One transmission plant achieved 90% recycling by installing multi-stage filtration - removing particulates, then oils, then dissolved solids. The purified water often exceeds municipal quality standards. The key lesson: treatment systems must match the specific contaminants present, requiring customized solutions at each facility.
Optimizing Cleaning Procedures
Traditional parts washing resembles a car wash - high-volume sprays constantly rinsing components. New approaches like laser ablation and CO2 snow cleaning eliminate water entirely for certain applications. Where water remains necessary, smart washers now use vision systems to target only dirty areas, reducing consumption up to 70%. These technologies prove that cleanliness and conservation aren't mutually exclusive.
Water-Efficient Design of Equipment
Equipment manufacturers now compete on water efficiency. Modern CNC machines feature dry-cutting options and mist-cooling systems that use minimal fluid. Paint booths incorporate air knives that strip excess water from parts for reuse. The most impressive innovations come from system redesigns - like one stamping plant that eliminated coolant by developing self-lubricating dies.
Monitoring and Measuring Water Usage
You can't manage what you don't measure - this adage drives the smart water revolution. Submetering every process, combined with real-time analytics, reveals surprising waste patterns. One engine plant discovered 20% of their water use came from a single misconfigured cooling tower. Such insights only emerge through comprehensive digital monitoring paired with human expertise.
Employee Training and Awareness Programs
Technology alone can't solve the challenge - people make the difference. Effective programs combine education with incentives. At a Volvo plant, workers proposed 127 water-saving ideas in one year, from fixing leaks to optimizing wash cycles. The best initiatives create water champions in each department, fostering friendly competition to find savings. This human element often delivers the fastest returns on investment.
Implementing Water Conservation Strategies Across the Supply Chain
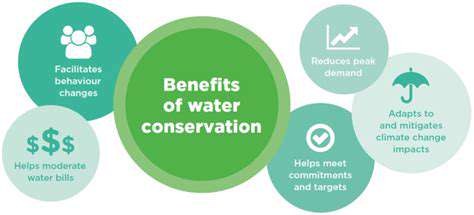
Water-Wise Landscaping Strategies
Industrial sites are rethinking grounds maintenance. Desert-adapted landscapes now surround many southwestern plants, reducing irrigation needs by 80% compared to traditional lawns. More innovative approaches use treated process water for irrigation, though careful monitoring prevents soil contamination. The most advanced facilities employ soil moisture sensors and weather-adaptive controllers to eliminate unnecessary watering.
Efficient Irrigation Systems
Modern industrial irrigation resembles precision agriculture. Drip systems target individual plants, while soil probes prevent overwatering. Some plants capture stormwater in retention ponds for later irrigation. The emerging frontier involves using plant species that thrive on minimally treated process water, creating virtuous cycles where wastewater becomes a resource.
Water Conservation Habits
Cultural change starts with visible leadership. At one Toyota plant, managers' offices display real-time water use dashboards. Another facility issues monthly water report cards to each department. Simple measures like low-flow fixtures and leak reporting apps engage all employees. The most effective programs tie conservation metrics to performance reviews, making water stewardship everyone's responsibility.
The Role of Innovation and Technological Advancement
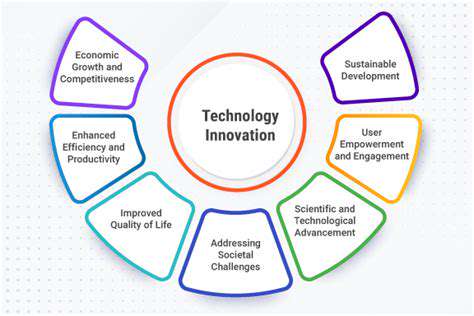
Innovation as a Catalyst for Progress
The water crisis demands breakthrough thinking. Biomimicry inspires some of the most promising solutions - like surfaces that mimic desert beetles to harvest atmospheric moisture. Other innovators look to space technology, adapting water recycling systems developed for Mars missions. Perhaps most exciting are digital water technologies that use machine learning to optimize every drop.
Technological Advancement and its Impact
Emerging technologies converge to solve water challenges. Advanced materials enable filters that remove contaminants at molecular levels. IoT sensors provide unprecedented visibility into water flows. Blockchain even finds application in tracking water stewardship across supply chains. These tools collectively enable the Industry 4.0 vision for water management - smart, connected, and radically efficient.
The path forward requires balancing innovation with implementation. Pilot projects prove concepts, but scaling demands collaboration across competitors. Industry consortia now share best practices, while universities partner with manufacturers on applied research. This cooperative spirit, combined with technological leaps, suggests a more water-efficient future is within reach.