Installation and Maintenance Tips for Long-Lasting Performance
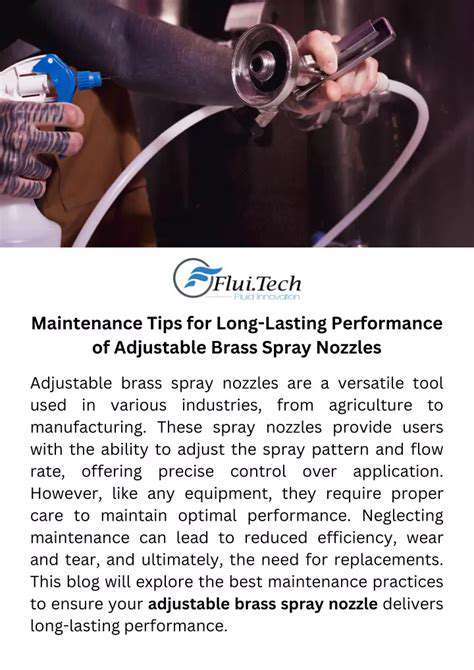
Pre-Installation Considerations
Before initiating the installation process, meticulous planning is crucial. A thorough site assessment is paramount to ensure the chosen location provides adequate support for the equipment and accommodates necessary utilities, such as power and drainage. Careful consideration of potential environmental factors, including temperature fluctuations and humidity levels, is essential to the long-term performance and longevity of the system. Properly identifying and addressing any potential obstacles early on will save considerable time and resources during the actual installation. Understanding the specific requirements detailed in the manufacturer's documentation is essential for successful installation.
Furthermore, coordinating with relevant stakeholders, such as building management or utility companies, is critical. This proactive approach ensures that necessary permits and approvals are secured prior to commencing work. Ensuring that all parties involved are aware of the project timeline and potential impact on operations helps to avoid unforeseen delays and complications throughout the process. Clearly outlining responsibilities and expectations for each party involved fosters a smooth and productive installation experience.
Installation Procedure
Adhering to the manufacturer's instructions is paramount during the installation phase. Following the step-by-step guidelines provided in the manual will help to ensure that the system is installed correctly and safely. This includes proper grounding procedures, which are crucial for avoiding potential safety hazards and ensuring compliance with local electrical codes. Thorough documentation of each step taken during installation is essential for future maintenance and troubleshooting.
Careful attention to detail is essential to prevent potential issues later on. Rigorous quality checks at each stage of the installation process are necessary to guarantee a secure and reliable system. This includes verifying proper connections, ensuring all components are correctly aligned, and confirming that all safety measures are in place. This proactive approach will minimize the risk of malfunctions and reduce the need for costly repairs.
Precise alignment of components, such as pipes or conduits, is vital for optimal performance and longevity. Incorrect alignment can lead to leaks, reduced efficiency, and premature equipment failure. Adhering to the specified tolerances and using appropriate tools is crucial for achieving precise alignment. This precision is critical to ensuring the system operates as intended and minimizes potential future maintenance requirements.
Maintenance Best Practices
Regular maintenance is crucial for maintaining the system's optimal performance and longevity. A well-defined maintenance schedule, adhering to the manufacturer's recommendations, is essential to address potential issues before they escalate. This includes routine inspections, cleaning, and lubrication of moving parts, and checking for any signs of wear and tear. Proactive maintenance will help to avoid unexpected breakdowns and costly repairs.
Implementing a comprehensive documentation system is key for tracking maintenance activities. Detailed records of all maintenance performed, including dates, tasks completed, and any observed issues, are invaluable for future troubleshooting and performance analysis. This historical data provides valuable insights into the system's overall health and helps to identify potential trends or patterns that may indicate future maintenance needs.
Staying current with the latest maintenance technologies and best practices is essential. Regularly reviewing industry updates and attending training sessions can help to identify new techniques and tools that can improve the efficiency and effectiveness of maintenance procedures. This continuous learning will ensure that the maintenance procedures remain aligned with the best practices of the industry, thereby ensuring the highest level of system performance and reliability.
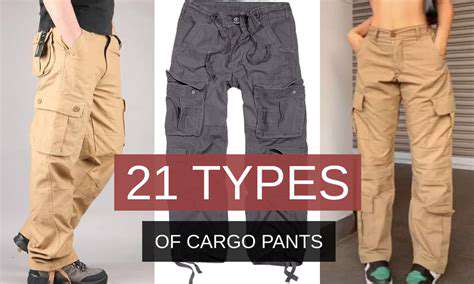