Overcoming Integration Hurdles in Modern Systems
Navigating Implementation Complexities
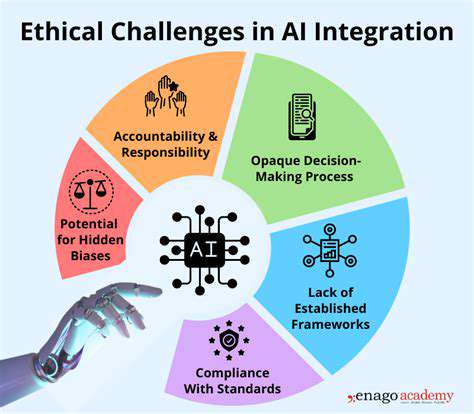
Practical Implementation Obstacles
Deploying unified systems frequently encounters substantial operational challenges. Strategic preparation and rigorous attention to technical specifications prove vital for project completion. The massive data quantities involved, coupled with ensuring interoperability among diverse platforms, can create substantial complications. Aligning resources and teams across multiple business units demands exceptional coordination skills and decisive management.
Furthermore, potential conflicts between new implementations and legacy infrastructure require thorough evaluation. Modernizing outdated systems often represents both technical and financial burdens. Evaluating effects on current operational procedures and creating detailed contingency plans helps reduce interruptions while enhancing staff acceptance rates.
Information Protection Priorities
Safeguarding confidential information remains critical for all integrated platforms. Advanced protective measures like end-to-end encryption, permission-based access, and periodic vulnerability assessments form the foundation for maintaining data security. Security incidents carry serious repercussions, affecting both corporate entities and their clients. Detailed threat analysis and preventive actions significantly decrease such risks.
Compliance with international privacy standards (including GDPR and CCPA) remains mandatory. Organizations must establish clear protocols for personal data acquisition, retention, and processing. Implementing data masking techniques where applicable supports both regulatory adherence and customer confidence.
Ensuring User Engagement
System effectiveness directly correlates with workforce acceptance and competence. Detailed instructional initiatives become indispensable for enabling personnel to properly operate upgraded platforms. Customizing educational content for various job functions and experience levels maximizes operational efficiency. Well-structured manuals and accessible helpdesk services provide essential ongoing assistance.
Addressing change resistance represents another critical factor. Transparent communication plans help alleviate concerns while securing stakeholder commitment. Fostering collaborative workspaces that encourage information exchange promotes technology adoption and sustains long-term operational benefits.
Legacy System Compatibility
Harmonious interaction with established platforms ensures smooth transitions and peak functionality. Technical specialists must dedicate substantial effort to prevent system conflicts and maintain data consistency. Recognizing integration pain points and formulating comprehensive connection blueprints proves essential, particularly when reconciling different software architectures and file structures.
Planning for Growth
Forward-looking design principles should guide all integration projects. Architectural decisions must incorporate expansion capabilities to accommodate organizational evolution. Preparing for anticipated developments like data surges or additional features often involves cloud technologies or component-based designs that simplify future modifications.
Building adaptable frameworks from initial development stages prevents expensive system replacements later. This proactive approach saves both financial resources and operational downtime during future scaling requirements.
Refining Manufacturing Operations
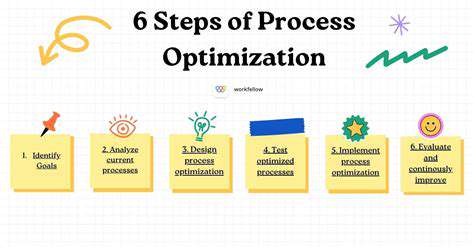
Workflow Rationalization
Manufacturing optimization initiatives typically commence with thorough process evaluations. Pinpointing congestion areas and operational inefficiencies enables targeted improvements. Detailed examination of each production phase reveals critical delay patterns requiring intervention. Well-structured operational sequences with unambiguous role definitions establish foundations for productivity gains and resource conservation.
Comprehensive procedure documentation enables accurate current-state analysis. Process mapping techniques highlight improvement opportunities while ensuring modifications remain evidence-based rather than speculative.
Material Logistics Enhancement
Efficient resource movement significantly impacts production continuity and output levels. From initial inventory receipt to final product distribution, material flow optimization reduces operational lag. Modernized handling systems produce measurable improvements in throughput rates and error reduction. Automation investments frequently yield substantial efficiency dividends across manufacturing environments.
Strategic storage solutions that maximize space utilization while ensuring material accessibility prove equally important. Concurrently, maintaining rigorous safety standards prevents workplace incidents during material transfer operations.
Waste Reduction Strategies
Lean manufacturing principles dramatically decrease operational waste while boosting customer value. Systematic elimination of non-essential activities across production cycles generates significant cost savings and capacity increases. This methodology emphasizes perpetual refinement and customer-focused process design.
Comprehensive waste analysis examines multiple categories including product defects, excess inventory, unnecessary movement, and underutilized personnel. Targeted interventions in these areas produce measurable efficiency improvements.
Technological Advancements
Modern production facilities increasingly rely on technical innovations. From robotic assembly to predictive analytics, these solutions enhance precision and output. Implementing smart manufacturing technologies enables instantaneous process monitoring and dynamic adjustments. This empirical approach to operational management supports continuous performance enhancement.
Advanced system integration improves product tracking and inventory control throughout manufacturing sequences. Careful technology evaluation ensures optimal solutions matching specific operational requirements and financial constraints.
Workforce Capability Building
Employee development investments yield substantial production benefits. Skilled operators demonstrate higher productivity and better adaptation to process changes. Comprehensive training programs equip staff with necessary competencies while promoting continuous improvement cultures. This approach frequently generates innovative process enhancement suggestions from frontline personnel.
Ongoing educational opportunities keep employees current with technological developments and revised procedures. Understanding broader production contexts enhances individual contribution quality and operational awareness.
Performance Measurement
Quantitative analysis validates optimization effectiveness. Tracking critical indicators like production volumes, equipment availability, and unit costs highlights improvement opportunities. Metric-based decision making ensures objective evaluation of process modifications. This analytical approach guides future refinement efforts and operational planning.
Regular performance reviews identify emerging trends and potential issues before escalation. Robust data infrastructure supports informed operational adjustments and preventive maintenance scheduling.