The Impact of Coil Spring Design on Ride Quality
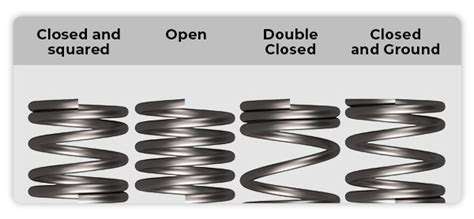
Coil Spring Design and Material Selection
When engineers select materials for coil springs, they must account for numerous performance factors to ensure durability and functionality. The chosen metal alloy must demonstrate exceptional tensile strength while resisting fatigue and corrosion over extended periods. Steel formulations with specific carbon percentages provide distinct advantages depending on the operational environment and load requirements. For applications demanding consistent performance under heavy cyclical loading, material science plays a decisive role in spring longevity.
Beyond basic material properties, the microstructure of spring alloys determines how energy transfers through the coil during compression and rebound. Metallurgists carefully tune these characteristics to create springs that maintain their shape after thousands of compression cycles while providing the necessary responsiveness for smooth operation. This attention to atomic-level details separates mediocre springs from exceptional ones.
Wire Diameter and Coil Dimensions
Mechanical engineers face a complex balancing act when determining wire thickness for coil springs. Thicker gauge wire increases structural integrity at the expense of added mass and material costs, while thinner wire reduces weight but may limit load capacity. The optimal diameter selection depends on precise calculations of expected forces and desired deflection characteristics.
Coil geometry equally impacts performance. Additional active coils create a more progressive spring rate, allowing for better absorption of road imperfections. Designers must consider both the number of coils and their pitch to achieve the perfect balance between comfort and stability. These dimensional decisions ultimately shape how vehicles respond to different driving conditions.
Free Length and Solid Length
Spring designers carefully calculate the unloaded dimensions to ensure proper operation throughout the full range of motion. The free length measurement determines how much the spring can compress before reaching its solid height, where adjacent coils make contact. Exceeding this limit causes coil bind, which creates harsh vibrations and can permanently damage suspension components.
Understanding the relationship between uncompressed and fully compressed states allows engineers to design springs that utilize their entire travel range without bottoming out. This becomes particularly important in performance applications where suspension travel is limited but must remain effective through extreme maneuvers.
Spring End Treatments
Termination methods significantly influence how springs interface with suspension components. Ground flat ends provide stable mounting surfaces, while specialized hooks or loops allow for specific attachment configurations. The finishing process at each end affects stress distribution, with poorly treated ends becoming failure points under repeated loading.
Specialized treatments like shot peening can enhance durability by creating compressive stresses at the surface. These processes help prevent micro-crack formation that could lead to catastrophic failures during operation. The choice of end treatment often depends on whether the spring will experience primarily compressive or torsional forces.
Spring Index and Load Distribution
The ratio between coil diameter and wire thickness establishes the spring's fundamental characteristics. A properly calculated index ensures forces distribute evenly across the entire spring rather than concentrating at specific points. This mathematical relationship directly affects how efficiently the spring stores and releases energy during operation.
Designers often use computer simulations to visualize stress patterns and optimize the index for particular applications. Suspension springs for heavy vehicles typically employ different indices than those designed for precision instruments, demonstrating how this parameter varies across industries.
Manufacturing Processes and Tolerances
Production methods leave an indelible mark on spring performance. Cold working processes increase strength through strain hardening, while heat treatment can relieve undesirable stresses. Modern CNC coiling machines achieve micron-level precision, maintaining consistency across mass-produced components.
Quality control measures verify that finished springs fall within specified tolerances for all critical dimensions. Advanced metrology equipment checks wire diameter consistency, coil spacing accuracy, and surface finish quality. These rigorous standards ensure each spring performs identically despite the challenges of metal forming processes.
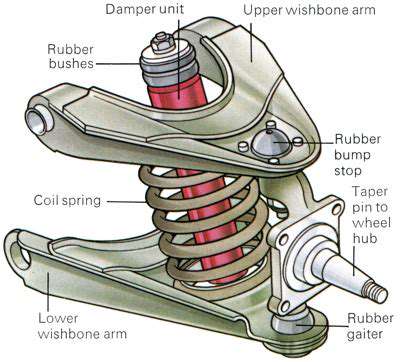