Protecting the Sensors and Perception Systems
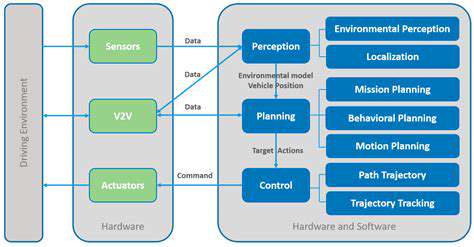
Protecting Sensor Integrity
In today's technology-driven world, where autonomous systems and industrial automation are becoming ubiquitous, the reliability of sensor data isn't just important - it's absolutely critical. Whether it's a self-driving car navigating busy streets or a manufacturing robot assembling precision components, these systems depend entirely on accurate sensor inputs to function correctly. Modern traction control systems, for example, would be completely ineffective without precise wheel speed sensor data.
Each type of sensor faces its own set of vulnerabilities that engineers must account for. Optical sensors, while incredibly useful, can be blinded by unexpected light sources or rendered useless by dust accumulation. Similarly, pressure sensors might give false readings if subjected to mechanical vibrations. The key to effective protection lies not just in choosing the right sensors, but in understanding their failure modes and designing appropriate safeguards. This might involve anything from specialized housings to advanced signal processing algorithms.
Maintaining Perceptual Accuracy
The challenge of keeping sensors accurate goes beyond just protecting them physically. Environmental conditions can dramatically affect how sensors interpret the world around them. A temperature sensor might give different readings at high altitude versus sea level, while a camera's perception of color can shift with changes in ambient lighting. Regular calibration isn't optional - it's a fundamental requirement for any system where sensor accuracy matters.
Forward-thinking engineers are now implementing continuous monitoring systems that track sensor performance in real-time. These systems can detect when a sensor starts to drift out of calibration and either compensate automatically or flag the issue for maintenance. This approach is particularly valuable in applications like medical diagnostics or aerospace, where sensor failures could have serious consequences.
Addressing Environmental Threats
Nature presents numerous challenges to sensor reliability. In arctic conditions, sensors might freeze or become brittle, while in tropical environments, moisture and salt air can corrode sensitive components. Electromagnetic interference from power lines or radio transmitters can create noise in electrical signals, potentially masking important data. The most effective protection strategies don't just react to these problems - they anticipate them during the design phase.
Modern sensor enclosures incorporate advanced materials that shield against multiple environmental threats simultaneously. Conformal coatings protect against moisture, Faraday cages block electromagnetic interference, and thermal management systems maintain optimal operating temperatures. These integrated solutions allow sensors to deliver consistent performance even in challenging conditions, whether they're mounted on deep-sea exploration vehicles or orbiting satellites.
Implementing Robust Data Validation
Even with perfect physical protection, sensor data needs thorough validation before it can be trusted. This process involves cross-checking readings against multiple sources and applying statistical methods to identify outliers. In autonomous vehicles, for instance, radar data might be compared with camera inputs to verify object detection. Without this critical validation step, even minor sensor errors could lead to dangerous situations.
The validation process must be customized for each application. Medical devices might use patient history to validate biometric readings, while industrial systems could compare sensor data with known process parameters. What matters most is establishing a comprehensive framework that catches errors before they can affect system performance. This often involves multiple layers of redundancy and sophisticated error-checking algorithms.