Introduction to Waste Heat Recovery in Automotive Manufacturing
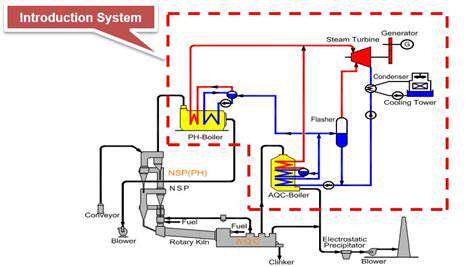
Understanding Waste Heat
Modern automotive plants generate vast amounts of thermal energy that often goes unused. Waste heat recovery (WHR) systems capture this valuable resource, transforming what was once considered an industrial byproduct into a strategic asset. These systems intercept thermal energy from multiple sources including exhaust streams, coolant loops, and equipment surfaces before it dissipates into the environment.
The automotive sector loses millions in potential energy savings annually through untreated waste heat. Forward-thinking manufacturers now recognize WHR as both an economic necessity and environmental imperative. When properly harnessed, this recovered energy can power auxiliary systems, preheat materials, or even contribute to facility-wide electricity generation.
Types of Waste Heat Recovery Systems
Automotive applications employ various WHR technologies tailored to specific thermal profiles. Heat exchangers dominate many installations, efficiently transferring thermal energy from exhaust gases to working fluids like water or thermal oils. More advanced systems incorporate organic Rankine cycles that convert lower-temperature waste heat into usable mechanical energy.
Regenerative thermal oxidizers represent another innovative approach, particularly for paint shop operations. These systems not only recover heat but also eliminate volatile organic compounds. The choice of technology depends on factors like temperature range, heat quality, and intended application - each plant requires a customized solution.
Applications of Waste Heat Recovery
In engine testing facilities, recovered heat preconditions test cells, reducing energy demands during cold starts. Paint curing ovens benefit from waste heat integration, slashing natural gas consumption by up to 30%. These applications demonstrate how WHR transforms energy liabilities into operational assets.
The most progressive plants now integrate WHR into their sustainability roadmaps, achieving both fiscal and environmental targets. Some facilities redirect recovered energy to district heating systems, creating additional revenue streams while reducing municipal carbon footprints.
Benefits and Considerations
WHR implementation delivers measurable ROI through reduced utility costs, often paying for installations within 2-3 years. Environmental benefits include lower greenhouse gas emissions and decreased reliance on fossil fuels. Proper system design must account for variable thermal loads and potential contaminants in waste streams.
Successful deployments require thorough energy audits to identify optimal recovery opportunities. Maintenance protocols must address fouling concerns in heat exchangers and ensure continuous system performance. When properly executed, WHR becomes a cornerstone of sustainable manufacturing practices.
Types of Waste Heat Sources in Automotive Plants
Internal Combustion Engine (ICE) Waste Heat
Engine testing stands as the most intensive waste heat source in automotive facilities. Dynamometer cells produce exhaust streams exceeding 600°C, containing sufficient energy to power entire support systems. Modern recovery solutions capture this energy through concentric pipe heat exchangers that maintain engine performance while extracting maximum thermal value.
The thermal profile varies significantly between gasoline and diesel platforms, requiring adaptable recovery solutions. Some installations now incorporate phase-change materials to handle transient thermal conditions during variable speed testing protocols.
Exhaust Gas Heat Recovery Systems
Turbo-compounding systems represent the cutting edge in exhaust energy recovery. These units employ secondary turbines to extract residual energy from exhaust flows, converting it directly to electrical power. When combined with traditional heat recovery, overall system efficiency improvements of 8-12% become achievable.
Transmission and Drivetrain Waste Heat
Component testing rigs for transmissions and differentials generate substantial thermal loads through mechanical friction. Advanced recovery systems now embed thermoelectric generators directly within test fixtures, capturing energy at the source. This approach minimizes thermal losses while providing real-time performance data.
Brake System Waste Heat
End-of-line brake testing produces intense but intermittent thermal pulses. Innovative plants employ thermal batteries to store and smooth this energy for consistent utilization. Ceramic heat exchangers withstand the extreme temperatures while preventing contamination of recovery loops.
Electric Motor and Power Electronics Waste Heat
EV component testing introduces new recovery challenges with lower-temperature but more consistent waste heat. Glycol-based systems efficiently capture this energy for facility heating applications. Some facilities now integrate motor cooling loops with building HVAC systems, creating closed-loop thermal management networks.
The Economic and Environmental Benefits of Waste Heat Recovery
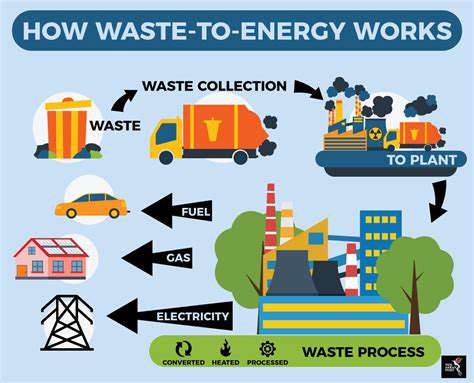
Sustainable Manufacturing Economics
Comprehensive WHR implementations typically reduce facility energy costs by 15-25%, with some plants achieving even greater savings. The payback period continues to shrink as energy prices rise and recovery technologies advance. Many operations now view WHR not as a capital expense but as a strategic investment with predictable returns.
Carbon Footprint Reduction
A single medium-sized automotive plant can eliminate 5,000-10,000 metric tons of CO2 annually through effective WHR. These reductions help manufacturers meet increasingly stringent environmental regulations while improving brand sustainability metrics. Some jurisdictions now offer carbon credit programs that provide additional financial incentives for WHR adoption.
Operational Resilience
Plants with robust WHR systems demonstrate greater energy independence, insulating operations from utility price volatility. During grid disruptions, recovered thermal energy can maintain critical processes, reducing downtime risks. This operational stability translates directly to bottom-line benefits.
Future Development Pathways
Emerging technologies like thermophotovoltaics promise to unlock new recovery opportunities from lower-grade heat sources. Industry collaborations are developing standardized WHR solutions that reduce implementation barriers for smaller manufacturers. These advancements ensure waste heat recovery remains a dynamic field with continuous improvement potential.