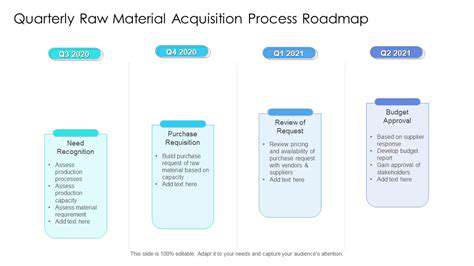
Raw Material Sourcing Strategies
Effective raw material acquisition is crucial for the success of any manufacturing process. This involves a multifaceted approach encompassing strategic sourcing decisions, supplier relationship management, and meticulous quality control measures. Identifying reliable and cost-effective suppliers is paramount to maintaining operational efficiency and minimizing production costs. Thorough due diligence is essential to evaluate potential suppliers, considering factors like their production capacity, quality standards, and ethical practices. This proactive approach ensures a consistent supply of high-quality raw materials, supporting the production timeline and overall profitability.
Developing strong relationships with key suppliers fosters collaboration and trust. This proactive engagement allows for open communication regarding potential challenges or fluctuations in material availability. Regular communication and joint problem-solving are essential for navigating supply chain disruptions and maintaining consistent material flow. Establishing clear contracts and performance metrics provides a framework for accountability and ensures that both parties are aligned on expectations. This collaborative approach ultimately strengthens the entire supply chain and reduces the risk of production delays.
Raw Material Preprocessing and Quality Control
Raw material preprocessing plays a vital role in ensuring the quality and consistency of the final product. This involves a range of processes, from cleaning and sorting to refining and transforming the raw material into a usable form. Careful attention to detail during each stage of preprocessing is critical to minimize waste and maintain product quality. Implementing rigorous quality control measures at each step of the preprocessing process is essential to prevent defects and ensure compliance with established standards.
Quality control procedures should encompass a variety of tests and inspections to guarantee that the preprocessed material meets the required specifications. This includes physical testing, chemical analysis, and microbiological evaluations. By meticulously monitoring and documenting the quality of each stage, manufacturers can proactively address potential issues and maintain consistent product quality, ultimately leading to a more reliable and trustworthy product. Maintaining detailed records of preprocessing steps and quality control results is essential for traceability and for identifying potential problems or areas for improvement.
Implementing stringent quality control protocols throughout the preprocessing stage minimizes the risk of defects and ensures that the final product meets the required standards. Regular audits and assessments of the preprocessing procedures help to identify any potential weaknesses or inefficiencies in the process. By continuously refining and optimizing the preprocessing procedures, manufacturers can improve overall product quality, reduce production costs, and enhance operational efficiency.
Robust documentation of each step in the preprocessing procedure is crucial for traceability and problem-solving. Detailed records of material handling, processing parameters, and quality control results provide valuable insights into the overall process. This data can be used to identify trends, pinpoint areas for improvement, and ultimately enhance the efficiency and effectiveness of the entire preprocessing operation.
Quality Control and Testing: Guaranteeing Performance and Safety
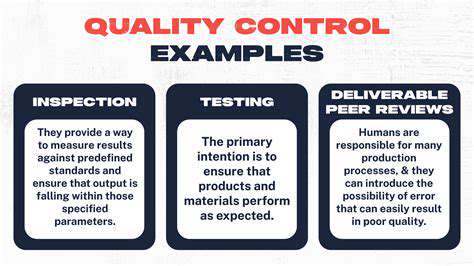
Quality Control Processes
Quality control (QC) is a critical aspect of any manufacturing process. It involves a systematic approach to identifying and eliminating defects in products or services before they reach the customer. Thorough QC procedures ensure consistent product quality, minimizing customer dissatisfaction and potential financial losses. This process typically includes various stages, from initial material inspection to final product testing.
Implementing robust QC processes requires careful planning and execution. This includes establishing clear standards and procedures, training personnel adequately, and using appropriate tools and equipment. Consistent adherence to these procedures is paramount for maintaining high quality standards.
Testing Methods
A range of testing methods are employed to evaluate the quality of products. These methods can be destructive or non-destructive, depending on the nature of the product and the type of information required. Non-destructive testing methods are often preferred when the product is expensive or fragile, or when repeated testing is necessary. Examples of testing methods include physical testing, chemical analysis, and visual inspection.
Choosing the appropriate testing method is crucial. The selected method should be capable of accurately assessing the product's characteristics and meeting the specific requirements of the product or service.
Importance of Statistical Analysis
Statistical analysis plays a vital role in quality control and testing. It helps to identify patterns, trends, and anomalies in data, allowing for more informed decision-making. By analyzing data, manufacturers can pinpoint areas needing improvement and adjust processes accordingly. Statistical methods such as control charts and process capability analysis are commonly used to monitor and improve quality.
Statistical analysis provides a systematic way to understand variability in the manufacturing process. This understanding helps to ensure that the process is operating within acceptable limits.
Guara's Quality Standards
Guara maintains stringent quality standards throughout its production process. These standards are meticulously documented and regularly reviewed to ensure they remain effective and relevant. Adherence to these standards ensures consistent quality across all products and maintains customer satisfaction. Guara's commitment to quality is evidenced in the positive feedback received from its customers.
Guara's stringent quality standards are backed by years of experience and a deep understanding of the industry's best practices.
Regulatory Compliance
Meeting regulatory requirements is an essential aspect of quality control and testing. Compliance with industry standards and regulations is crucial for ensuring product safety, efficacy, and legality. Guara meticulously adheres to all relevant regulations to protect consumer health and safety and to maintain its reputation.
Failure to comply with regulations can result in significant penalties and reputational damage. Thus, consistent monitoring and adherence to regulatory guidelines are paramount.
Continuous Improvement
Guara is committed to continuous improvement in its quality control and testing procedures. This commitment involves a dedicated effort to identify areas for improvement and implement changes to enhance efficiency and effectiveness. Regular reviews and feedback from various stakeholders, including customers and employees, are crucial in this process. By continuously refining its procedures, Guara strives to maintain its competitive edge in the market.
Continuous improvement is a dynamic process that demands ongoing evaluation and adaptation to meet evolving market demands and customer needs.
Data Management and Reporting
Effective data management and reporting are essential for quality control and testing. Comprehensive data collection and analysis enable manufacturers to identify trends, pinpoint areas for improvement, and ultimately enhance product quality. Guara meticulously documents all test results and quality control procedures for future reference and analysis.
Thorough documentation and reporting allow for effective tracking of quality issues and enable data-driven decision-making to improve processes and products.