Coastal environments amplify these risks—salt-laden air corrodes metals rapidly. Engineers combat this by selecting alloys like marine-grade stainless steel or applying multi-layer protective finishes. Such measures demonstrate how environmental awareness shapes durable designs.
Materials Science and Engineering Principles
Breakthroughs in materials science continuously redefine durability. From self-healing polymers to carbon-fiber composites, innovation delivers unprecedented resilience. These advancements not only prolong product life but also curb environmental harm by reducing replacement frequency.
Hybrid materials exemplify this progress. By layering ceramics with metals, engineers create components resistant to both impact and heat—ideal for aerospace applications. Such composites exemplify how material optimization drives reliability in demanding environments.
The synergy between material properties and thoughtful design remains the cornerstone of enduring products.
Maintenance and Care Requirements
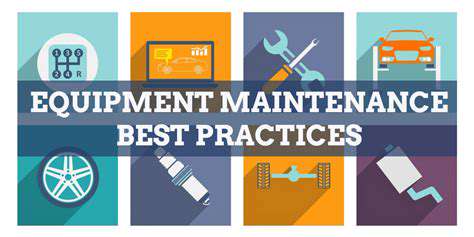
Essential Maintenance Practices
Proactive maintenance separates reliable equipment from costly breakdowns. Regular inspections catch worn components before they fail, while calibrated adjustments ensure peak efficiency. Neglecting minor issues—like a frayed belt—can cascade into system-wide failures.
Documented maintenance logs reveal patterns: a motor requiring frequent bearing replacements might need redesign. This data-driven approach minimizes downtime and optimizes resource allocation across operations.
Cleaning and Sanitizing Procedures
In food processing plants, sanitation isn't optional—it's regulatory. Steam-cleaning protocols remove biofilm buildup in pipes, while UV sterilization chambers disinfect packaging lines. These measures prevent contamination recalls that can devastate brands.
Electronics demand different care; static-free wipes preserve circuit boards, while compressed air clears vents without moisture damage. Tailoring methods to each system maximizes both hygiene and equipment life.
Lubrication and Greasing Requirements
Precision lubrication extends machinery life dramatically. Over-greasing bearings attracts debris, while under-lubrication causes metal-on-metal wear. Automated lubrication systems now monitor conditions in real-time, dispensing exact amounts when sensors detect increased friction.
In subzero environments, synthetic lubricants outperform conventional oils by resisting viscosity changes. This adaptation prevents equipment seizure during Arctic winters.
Troubleshooting and Problem-Solving
Effective troubleshooting combines technical knowledge with systematic analysis. Thermal imaging cameras pinpoint overheating components invisible to the naked eye, while vibration analysis predicts bearing failures weeks in advance.
Cross-training maintenance teams ensures diverse perspectives—an electrician might spot wiring issues a mechanic would overlook. This collaborative approach resolves complex faults faster.
Storage and Handling Procedures
Climate-controlled storage preserves sensitive instruments. Rubber seals degrade in humidity, while extreme cold embrittles plastics. Desiccant packs and temperature logging maintain optimal conditions during storage.
Proper handling techniques prevent costly damage—forklift operators trained in load balancing avoid structural stresses on stored items. Such protocols are especially critical for aerospace components where microscopic flaws can have catastrophic consequences.
Safety Precautions and Regulations
Lockout-tagout procedures save lives. When servicing industrial presses, physical locks prevent accidental activation during maintenance. Recent IoT advancements enable digital lockout systems that alert entire teams when equipment enters service mode.
Regulatory compliance evolves constantly—OSHA's updated fall protection standards now require more frequent harness inspections. Staying current through continuous training prevents both injuries and fines.
Environmental Impact and Sustainability
Environmental Considerations
The ecological footprint of vehicle finishes involves complex trade-offs. Traditional paints release VOCs during application—these airborne chemicals contribute to smog formation and respiratory illnesses. Waterborne paints offer a partial solution, though they still require energy-intensive production.
Vinyl wraps present different challenges. While installation emits fewer VOCs, the PVC-based films aren't biodegradable. Emerging plant-based wrap materials show promise, decomposing within years rather than centuries in landfills.
Sustainability Practices
Lifecycle analysis reveals surprising insights. A high-quality paint job lasting 15 years may ultimately out-sustain wraps needing replacement every 5 years. However, removable wraps allow color changes without stripping layers, reducing material waste over time.
Innovative recycling programs now grind old wraps into pellets for manufacturing new products. Combined with solar-powered production facilities, these circular economy approaches are reshaping the industry's environmental impact.
The most sustainable choice varies by use case—fleet vehicles benefit from wraps' reparability, while collectors' cars may favor durable ceramic coatings. Transparency in supply chains helps consumers make informed ecological decisions.