Introduction to Energy Management in Automotive Manufacturing
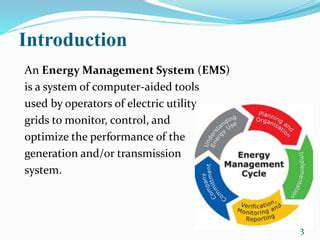
Understanding Energy Consumption
The foundation of effective energy management lies in comprehensively tracking and analyzing energy usage patterns across facilities. Manufacturing plants must establish precise metrics to measure consumption at each production stage. Without accurate baseline data, any optimization efforts become guesswork rather than science. Modern facilities employ advanced metering infrastructure to capture real-time data from every energy-consuming asset.
This diagnostic phase often reveals surprising insights - for instance, how non-production hours still account for 15-20% of total energy use due to standby loads. Such discoveries fundamentally reshape energy conservation strategies. The most successful implementations combine automated monitoring with manual verification walks to validate the data.
Identifying Energy Waste
Energy waste manifests in numerous forms, from compressed air leaks costing thousands annually to outdated motors running at constant speeds regardless of load. The most effective audits employ thermal imaging alongside power quality analyzers to detect both obvious and hidden inefficiencies. Surprisingly, many facilities find their greatest savings come from correcting power factor issues rather than equipment upgrades.
One automotive plant discovered their paint shop consumed 40% more energy than industry benchmarks. This revelation prompted a complete process redesign that paid for itself in 18 months. The key was correlating energy spikes with specific production activities through minute-by-minute analysis.
Implementing Energy-Efficient Technologies
While LED lighting grabs headlines, the most impactful upgrades often involve industrial systems. For example, variable frequency drives on large motors can reduce energy use by 30-50%. The latest regenerative braking systems on overhead cranes actually return energy to the grid during descent. These technologies create compounding benefits - reduced energy demand lowers cooling requirements for the entire facility.
Optimizing Operational Practices
Behavioral changes frequently deliver faster returns than capital projects. Simple measures like implementing shutdown checklists can eliminate 10-15% of energy waste overnight. The most successful programs train employees to become energy detectives, rewarding teams that identify waste patterns. One BMW plant saved €2 million annually just by optimizing their compressed air system schedule.
Advanced facilities now use digital twins to simulate different operating scenarios before implementation. This virtual testing prevents costly trial-and-error in the physical plant. The simulations often reveal non-intuitive optimal settings that human operators would never discover independently.
Monitoring and Evaluating Results
True energy management requires closing the feedback loop. The best systems compare predicted savings against actual results down to the individual machine level. This granular verification uncovered an interesting phenomenon at a Toyota plant - energy savings from new equipment often exceeded specifications because operators became more conscientious about usage.
Continuous improvement cycles should incorporate both automated alerts and quarterly deep-dive analyses. This dual approach catches both sudden anomalies and gradual efficiency erosion. Many plants establish energy war rooms displaying real-time performance dashboards to maintain focus.
Financial Benefits and ROI
Beyond direct utility savings, energy efficiency improves operational resilience. Plants with robust energy management systems weathered recent energy price spikes with minimal disruption. The financial case strengthens further when considering extended equipment lifespan and reduced maintenance costs from optimized operation.
Forward-thinking manufacturers now treat energy as a variable cost center rather than a fixed expense. This mindset shift unlocks opportunities that traditional accounting methods overlook. Some facilities achieve negative-cost efficiency measures by creatively bundling incentives and operational improvements.
Optimizing Power Consumption in Production Lines
Minimizing Idle Time and Energy Waste
Production line optimization begins with mapping energy flows throughout the manufacturing process. Sophisticated plants now instrument every workstation with power monitors, creating a detailed energy fingerprint for each production step. This analysis frequently reveals that 20-30% of energy consumption occurs during non-value-added intervals.
The most advanced solutions employ machine learning to predict optimal equipment sequencing. For example, Volkswagen's Smart Production initiative uses AI to coordinate robot movements, reducing peak demand charges by 18%. Such dynamic scheduling would be impossible without real-time energy visibility at the device level.
Leveraging Efficient Equipment and Technologies
Equipment selection criteria now emphasize total cost of ownership rather than just purchase price. The latest servo presses demonstrate how advanced technology can slash energy use by 60% while improving precision. Pneumatic systems are increasingly being replaced with electric alternatives that offer better controllability and efficiency.
Emerging technologies like magnetic bearings and superconducting motors promise even greater savings. These innovations often pay back faster than expected due to their secondary benefits, such as reduced vibration extending tool life. The key is piloting new technologies in non-critical applications before full deployment.
Implementing Smart Energy Management Systems
Modern energy management platforms have evolved beyond simple dashboards. The newest systems integrate with production planning software to optimize energy usage against production schedules. They can automatically shift non-critical processes to off-peak hours or temporarily reduce ventilation during lulls in activity.
Predictive capabilities represent the next frontier. By analyzing equipment performance trends, these systems can schedule maintenance before efficiency degrades. Bosch's Industry 4.0 implementation achieved a 7% energy reduction purely through smarter maintenance timing.
Waste Heat Recovery and Energy Recycling
Innovative plants are turning waste streams into assets. Fiat Chrysler's Sterling Heights plant recovers enough heat from paint ovens to warm the entire facility in winter. Such systems often achieve payback periods under three years thanks to rising energy costs.
The circular economy concept extends to utilities as well. Advanced facilities now achieve 90% recycling rates for compressed air and process water. These closed-loop systems not only save energy but also reduce environmental permitting challenges. The most progressive designs incorporate energy storage to balance intermittent renewable generation.
Leveraging Data Analytics for Enhanced Energy Management
Data Collection and Integration
The quality of energy analytics depends entirely on data foundation. Leading manufacturers now deploy IoT sensors at unprecedented density - sometimes hundreds per production line. This granularity enables fascinating insights, like how machine orientation affects cooling loads.
The integration challenge lies in harmonizing data from legacy equipment with modern systems. Middleware solutions that normalize data streams without requiring equipment upgrades are proving invaluable. Ford's big data platform now ingests over 50 different data types to create a unified energy picture.
Predictive Modeling for Optimization
Advanced simulation tools can forecast the energy impact of production changes with 95% accuracy. GM uses digital twins to test energy scenarios before implementing physical changes, avoiding costly trial-and-error. These models become increasingly precise as they ingest more operational data.
The most sophisticated implementations incorporate weather forecasts and energy market prices. This allows plants to dynamically adjust production schedules based on expected solar generation or electricity costs, creating substantial financial advantages.
Real-Time Monitoring and Alerting
Modern alert systems have moved beyond simple threshold alarms. AI-driven anomaly detection can identify emerging issues before they become problems, like detecting bearing wear through subtle power signature changes. This predictive capability prevents both energy waste and unplanned downtime.
The most effective implementations route alerts based on severity and expertise required. Tesla's system automatically dispatches the appropriate technician based on the anomaly pattern, dramatically reducing resolution time.
Statistical Analysis and Trend Identification
Long-term trend analysis reveals patterns invisible in daily operations. Detailed analysis at a BMW plant showed that energy use per vehicle actually increased after efficiency upgrades - because operators became less vigilant. This counterintuitive finding led to revised training protocols.
Developing Actionable Insights and Recommendations
The true test of analytics is implementation. Nissan's Kaizen Energy program translates findings into standardized work instructions, ensuring insights become permanent improvements. The most successful programs create feedback loops where operators suggest new data points to monitor.
Benchmarking and Performance Comparisons
Smart benchmarking goes beyond simple metrics. Volvo's plant-to-plant comparisons account for differences in product mix and climate, creating fair comparisons that drive meaningful improvement. The best programs share learnings across facilities while respecting competitive dynamics.
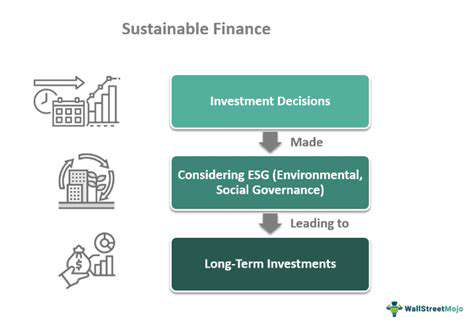